Choosing the Right CNC Machine for Your Project
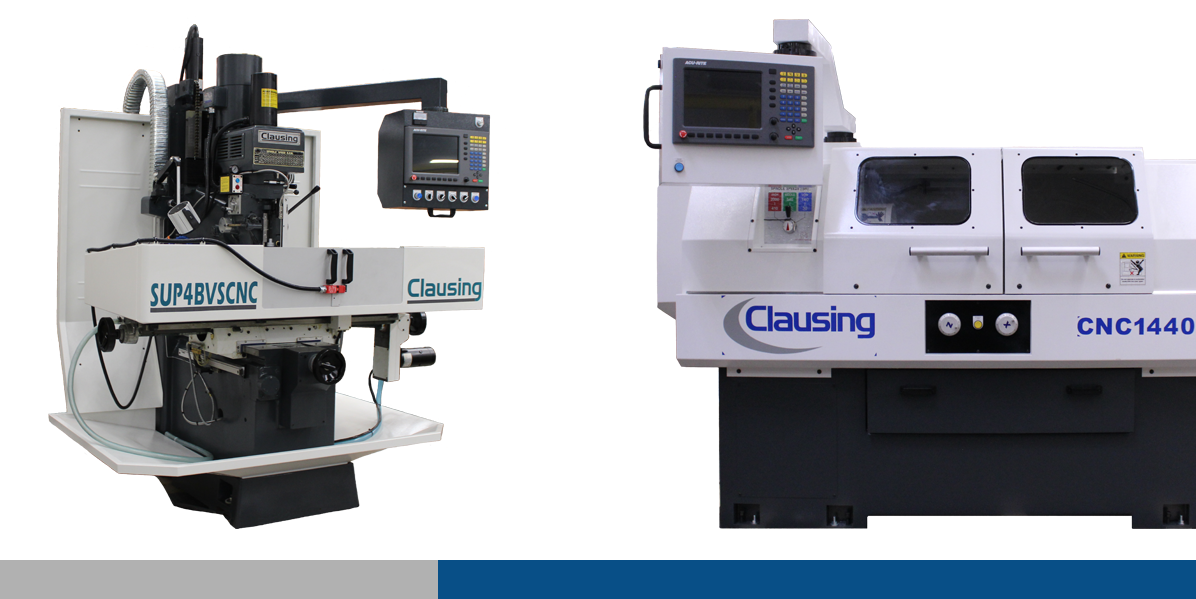
Introduction
Selecting the right CNC machine for your project is vital for achieving the desired results efficiently and cost-effectively. Whether you’re working on small-scale prototypes or large-scale production runs, the machine you choose can greatly impact the quality and speed of your work.
First, it’s essential to assess your project’s requirements. Understanding the types of materials you will be using, the complexity of your designs, and the volume of production can help you narrow down your options. Different CNC machines are optimized for different tasks, so identifying your needs will guide you to the most suitable machine.
Next, evaluating the technical specifications of potential CNC machines is crucial. Factors like spindle speeds, working capacity, travels, and precision can greatly affect your project’s outcome. Each project has unique demands, and matching these specifications to your needs ensures that your machine will perform efficiently and accurately.
Finally, considering software compatibility and budget constraints will help finalize your decision. Software plays a significant role in the functionality of CNC machines, influencing ease of use and integration with current systems. Balancing the initial investment against long-term maintenance costs and potential returns will ensure that you choose a machine that offers value.
Assessing Your Project Requirements
Determining material types is the first step in choosing the right CNC machine. Different materials require varying levels of power and precision. For instance, if you are working with metals like Steel and Titanium, you will need a machine with a robust spindle and high cutting force. Alternatively, for materials like Aluminum or Copper, a lighter machine with lower power may be adequate. Identifying the primary materials for your projects helps you select a CNC machine tailored to those specific needs.
Understanding project complexity is also essential. Simple designs with straight cuts and drilled holes may not require an advanced machine. However, intricate designs with detailed engravings and multiple dimensions might require a more sophisticated CNC machine. Consider the design software’s compatibility and whether it supports the complexity of your projects. Machines with higher precision and versatile capabilities ensure that even the most complicated designs are executed flawlessly.
Estimating production volume guides you in choosing a machine that matches your output needs. For large-scale production, you need a CNC machine that can handle continuous operation without compromising quality. High-volume projects require machines with greater durability and efficiency. On the other hand, for smaller, custom jobs, a machine optimized for short runs and quick changeovers might be more suitable. Assessing your expected production volume helps you find a machine that balances speed, quality, and capacity.
Evaluating Machine Specifications
Spindle speed and power are critical factors to consider when evaluating CNC machines. In a CNC milling machine, the spindle is responsible for rotating the cutting tool, but on a lathe, it is typically responsible for rotating the workholding. Machines with powerful spindles can handle tougher materials and more demanding cuts. Choose a machine with the right balance of speed and power based on the materials and tasks you anticipate.
Work area dimensions determine the size of the projects you can undertake. A larger work area allows you to machine bigger pieces or multiple smaller pieces simultaneously.
On a CNC lathe, you’ll need to assess the “swing over bed” specification, which is in direct correlation to the largest diameter workpiece that can be fit on the machine. The distance between centers specification refers to the length of the bed. On a CNC Mill, however, it should be about the table size, weight rating, travel, and capacity.
Ensure that the CNC machine you choose has a sufficiently large work area to accommodate your typical project sizes. This helps you avoid limitations in your project scope and ensures efficient use of the machine’s capabilities.
Precision and accuracy are paramount for producing high-quality parts. CNC machines are known for their ability to produce exact replicas repeatedly, but the level of precision varies between models. Evaluate the machine’s tolerance or the degree to which your final product can vary from the designed specifications. For projects requiring tight tolerances and high accuracy, go for a machine that offers excellent precision. Ensuring high precision means your final products will consistently meet the desired standards, reducing waste and rework.
Considering Software and Compatibility
The importance of software support is a key factor when choosing a CNC machine. The right software can influence the ease with which you design and execute projects. Look for machines that come with user-friendly design software that fits your project needs. Good software support also means that you have access to updates and technical help, ensuring your machine stays up-to-date and functional.
Compatibility with existing systems is crucial for a smooth workflow. If you’re already using specific CAD (Computer-Aided Design) or CAM (Computer-Aided Manufacturing) software, make sure your new CNC machine can integrate seamlessly with these programs. This compatibility can save you time and money, reducing the learning curve for your team and minimizing disruptions in production. Ensure that the machine’s software system aligns with what you currently have to prevent any compatibility issues.
Ease of use and learning curve affect how quickly you can start using your CNC machine efficiently. Some machines come with more intuitive interfaces and simpler programming languages, which can be beneficial if your team is new to CNC technology. Machines with complex software might offer more features but could require extensive training to operate effectively. Look for a balance between ease of use and functionality that suits your team’s skill level and your project requirements.
Budgeting and Cost Analysis
Initial investment vs long-term costs should be carefully assessed. The price of a CNC machine goes beyond the initial purchase. Consider the machine’s durability, the cost of consumables such as cutting tools and lubricants, and whether any accessories are needed. High-quality machines might have a higher upfront cost but offer better longevity and efficiency, making them more cost-effective in the long run.
Evaluating maintenance expenses is important to understand the true cost of owning a CNC machine. Regular maintenance is necessary to keep the machine running smoothly and to prevent expensive repairs. Look into the cost and availability of spare parts and whether the manufacturer offers a maintenance plan. Some machines may require more frequent servicing, which can add to the overall cost. A well-documented maintenance plan helps you budget for these ongoing expenses.
Return on investment (ROI) is the ultimate measure of a CNC machine’s value. Determine how quickly you can recoup your initial costs through increased production efficiency and quality. Consider factors such as reduced waste, faster turnaround times, and the ability to take on more complex projects. A higher upfront investment might be justified if it leads to significant long-term gains. Calculate your expected ROI to ensure the machine you choose will be a worthwhile addition to your operations.
Conclusion
Choosing the right CNC machine for your project involves a detailed analysis of requirements, specifications, software compatibility, and budget. By thoroughly assessing the types of materials you’ll work with, the complexity of your projects, and your production volume, you can narrow down your options. Evaluating the technical specifications ensures the machine matches your project needs in terms of spindle speed, work area dimensions, and precision. Considering software compatibility and ease of use helps integrate the machine smoothly into your workflow without major disruptions.
Budgeting and cost analysis go beyond the initial investment, including maintenance expenses and evaluating the long-term return on investment. A machine that’s cost-effective in the long run can offer better value, even if the initial price is higher. Evaluating all these factors ensures you make a well-informed decision that meets your project needs efficiently and economically.
At Clausing, we understand the unique challenges of choosing the right CNC machinery. Contact us today to explore our wide range of CNC machines designed to meet various industrial applications. Let us help you find the perfect machine to optimize your production process and achieve outstanding results.
October 15, 2024 | Views | Categories: Article, CNC Machines, Guide, Tips
Related Posts
Latest Posts
Categories
Article
Guide
Tips
Topics
CNC Machines
Standard Machines
Tags
Clausing
CNC Lathes